Auxiliary switches play a vital role in modern industrial and domestic equipment. They not only ensure the stable operation of the system, but also provide the necessary safety in the event of a malfunction. However, even the most reliable devices can encounter problems. So, how should we react when faced with an auxiliary switch failure situation? This article will explore this topic in depth.
First, we need to understand the basic functions and common types of failure of auxiliary switches. Auxiliary switches are usually used to control the opening and closing of the circuit, as well as to send signals in some cases. Common failures include poor contact, mechanical wear, or shorted circuits. According to industry statistics, poor contact is the most common cause of auxiliary switch failures, accounting for up to 60% of all failures.
Once an
auxiliary switch is found to be malfunctioning, the first and foremost treatment is to disconnect the power and check. Safety always comes first, so make sure that the power supply in question is completely disconnected before beginning any repair work. This step is a key measure in preventing electrocution.
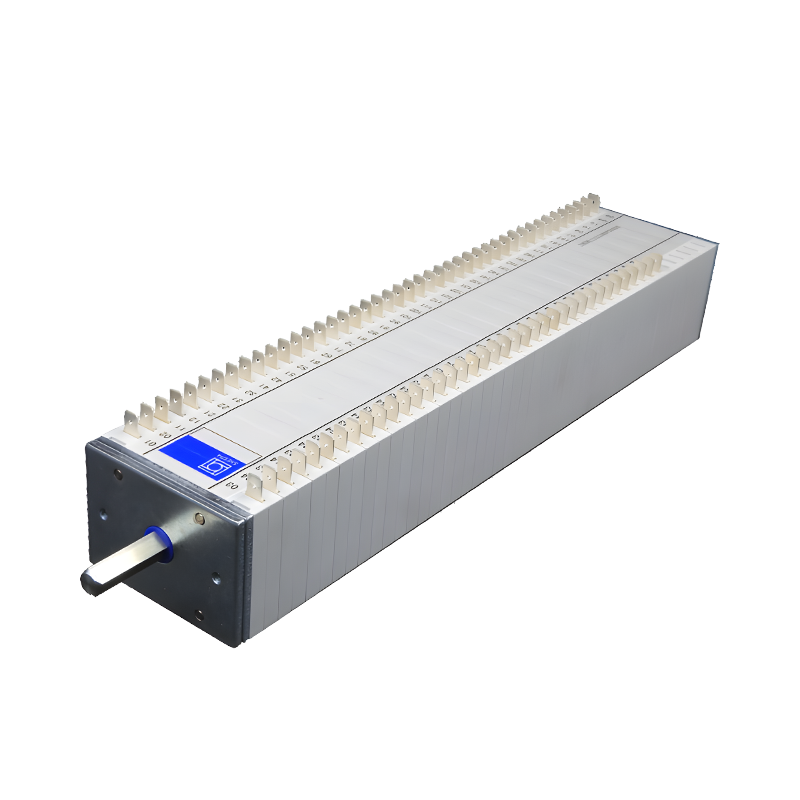
Subsequently, perform a visual inspection of the auxiliary switch. Look for any signs of corrosion, foreign objects stuck in the switch or loose wiring. These are usually the direct cause of switch failure. According to electrical repair manuals, more than 50 percent of failures can be resolved by simply cleaning and reconnecting the wiring.
If a visual inspection fails to reveal the problem, the next step is to use a multimeter to check the switch's connectivity and resistance. The proper way to do this is to set the multimeter to the proper range and measure each end of the switch. Normally, the switch should show a very low resistance value when closed and close to infinity when disconnected. Data indicate that about 30% of all faults can be diagnosed by this method.
When none of the above methods solve the problem, it may be necessary to replace the auxiliary switch. Select a new switch that matches the prototype model and be sure to install it according to the manufacturer's instructions. Statistically, equipment uptime can be increased to over 95% with a new switch.
Finally, to prevent future failures, regular maintenance checks are recommended. This includes checking that the wiring is secure, cleaning out dust and dirt, and testing the function of the switch. With preventive maintenance, the failure rate can be significantly reduced.

To summarize, when confronted with the handling of
auxiliary switches in case of malfunction, we should take a series of orderly steps: power failure inspection, visual inspection, testing with a multimeter and, if necessary, replacing the switch with a new one. Through these methods, we can effectively solve most fault problems. Meanwhile, regular maintenance is also the key to ensure the long-term stable operation of auxiliary switches.