Injection molding plays an important role on the precision manufacturing stage. Like a dancer's every jump and spin on stage, the quality of injection molded parts directly affects the performance and aesthetics of the final product. However, warpage occurs from time to time, and like an uninvited shadow, it silently erodes the perfection of manufacturing. How to dispel this shadow and optimize our molds has become the key to improving the
injection molding process.
Warpage, a common problem in injection molding, stems from the inherent characteristics of plastic materials and the complexity of the process. Plastic shrinks when it cools, and if the shrinkage is not uniform, it will result in a distorted shape of the finished product, which is what we call warpage. To solve this problem, we must have an in-depth understanding of its causes, and from the mold design, material selection, processing parameter settings, and other aspects of the start, a comprehensive optimization.
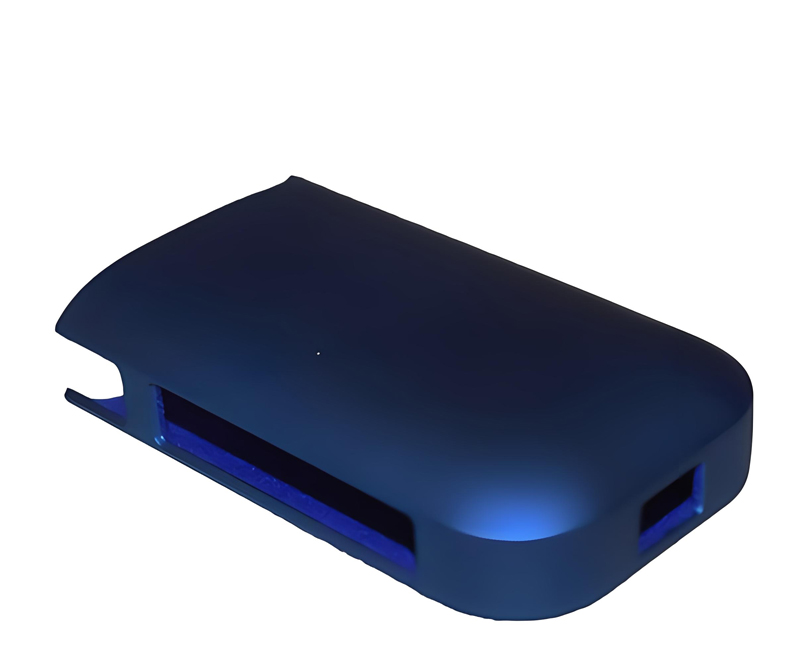
Mold design is the basis for solving the warpage problem. Designers need to use their excellent skills and profound knowledge to ensure that the temperature control system of the mold can achieve fast and uniform heating and cooling. Through computational fluid dynamics analysis, we can predict the flow and cooling of the plastic melt in the mold cavity, and accordingly adjust the location and size of the gates, as well as the layout of the cooling channels, in order to reduce the internal stresses caused by temperature differences.
The choice of material is also crucial. Different plastics have different coefficients of thermal expansion and shrinkage, and choosing the right material can radically reduce the possibility of warpage. In addition, the use of fiber-reinforced materials or the addition of appropriate fillers can also improve the dimensional stability of the finished product.
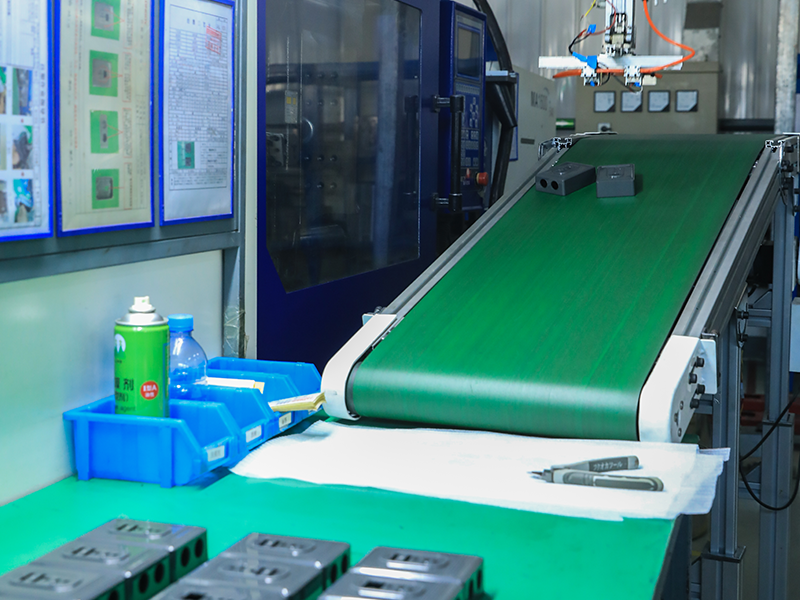
In the setting of processing parameters, we need to control them as finely as debugging a precision instrument. Injection speed, pressure, holding time, mold temperature, etc., each parameter needs to be carefully adjusted to ensure that the plastic melt can fill the mold cavity under optimal conditions and remain as uniform as possible during cooling.
In practice, we can use mold flow analysis software for simulation to find out the best combination of processing conditions through virtual tests. This scientific method not only predicts the occurrence of warpage, but also guides us to make adjustments in actual production.
However, there is always a gap between theory and practice. In actual operation, we still need to test and correct continuously. Through the trial-and-error method, we gradually approach the best processing program. Each adjustment is a deepening understanding of the knowledge of mold optimization, and each improvement is an enhancement of product quality.
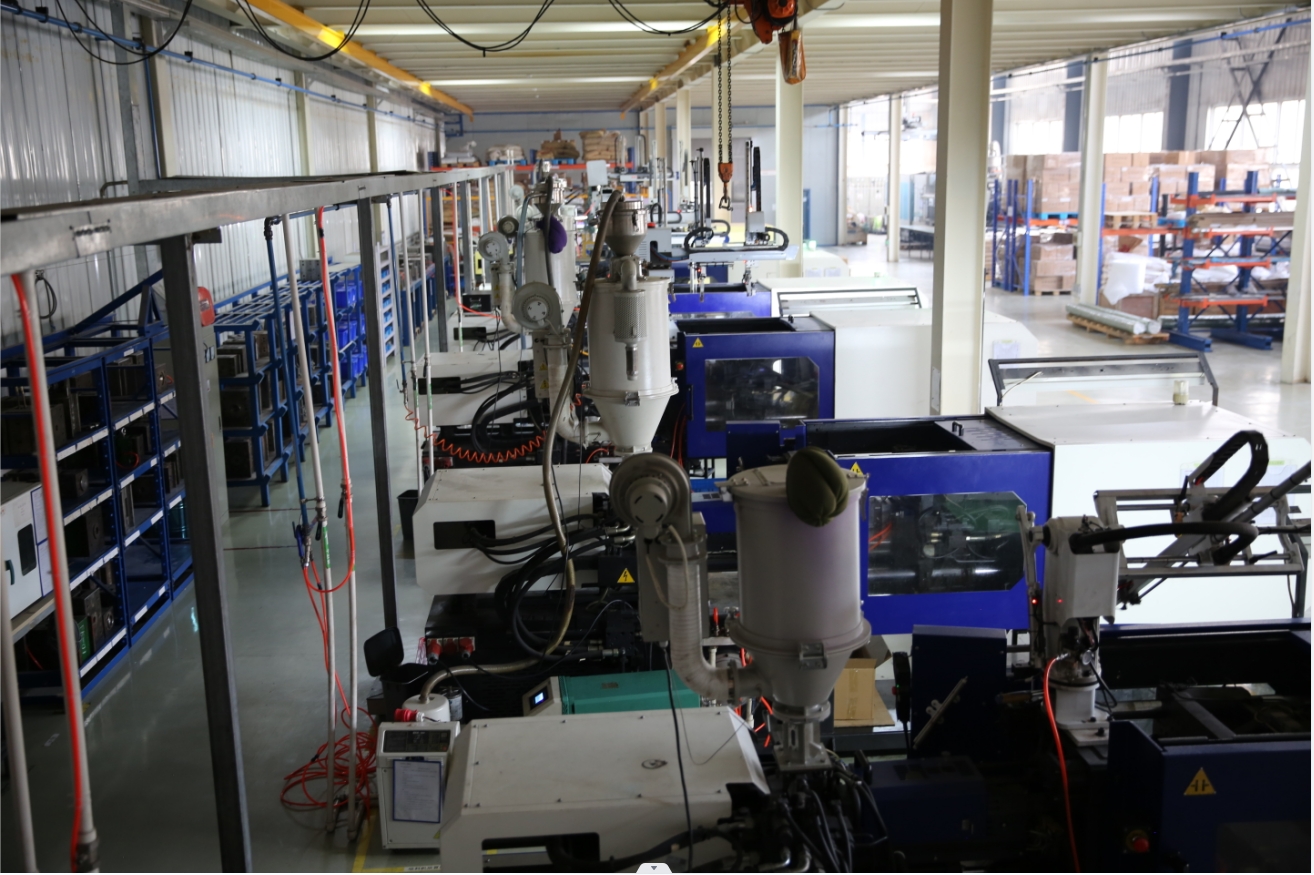
The solution to the warpage problem is not an overnight solution, it requires engineers' wisdom and patience, a deep understanding of the material properties and a fine control of the processing technology. In this battle with warpage phenomenon, we keep exploring and innovating, and finally, we will win the victory and produce impeccable injection molded products.
This is a dance of technology and wisdom, every rotation is full of challenges, every jump contains opportunities. On the road of optimizing moulds, we persist and strive for excellence until every
injection moulded part can be like a perfect work of art, showing their due elegance.