In the world of
injection molding processing, every detail is critical. From the selection of raw materials to the design of the mold to the shaping of the final product, each step requires precise control and in-depth understanding. However, of all the details, two in particular are critical - that is injection time and holding time. These two factors not only affect the quality of the product, but also determine production efficiency and cost.
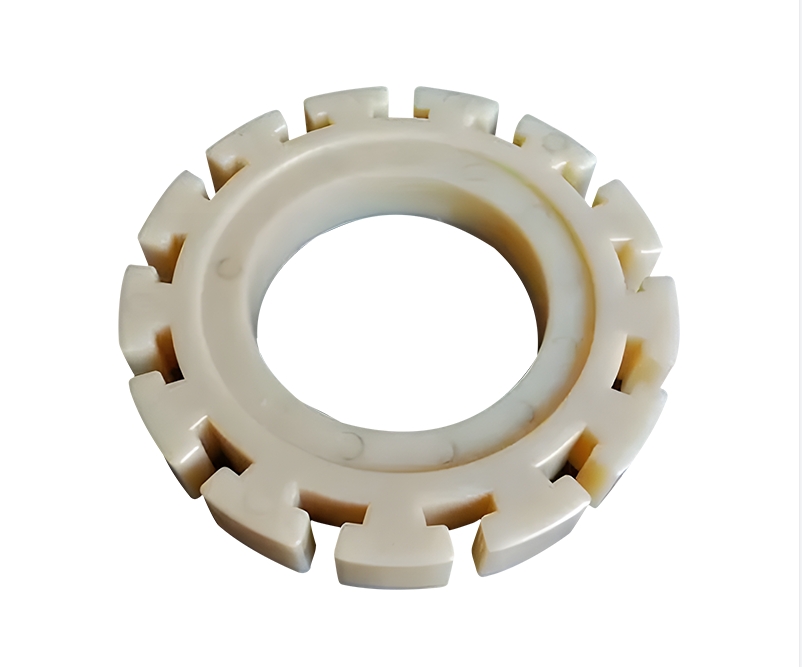
Injection time
Injection time, in simple terms, is the time it takes for the plastic melt to be injected into the mold. This time needs to be long enough to ensure that every corner of the mold is filled, but short enough to prevent the plastic from overheating or breaking down. Finding this balance isn't easy, but when it is, it ensures a quality product.
Too long an injection time can cause the plastic to flow excessively through the mold, which may create problems with flying edges, warping, or excessive internal stress. Too short an injection time, on the other hand, can lead to short shots, where the mold is not completely filled, which can have a direct impact on the functionality and appearance of the product.
Holding Time
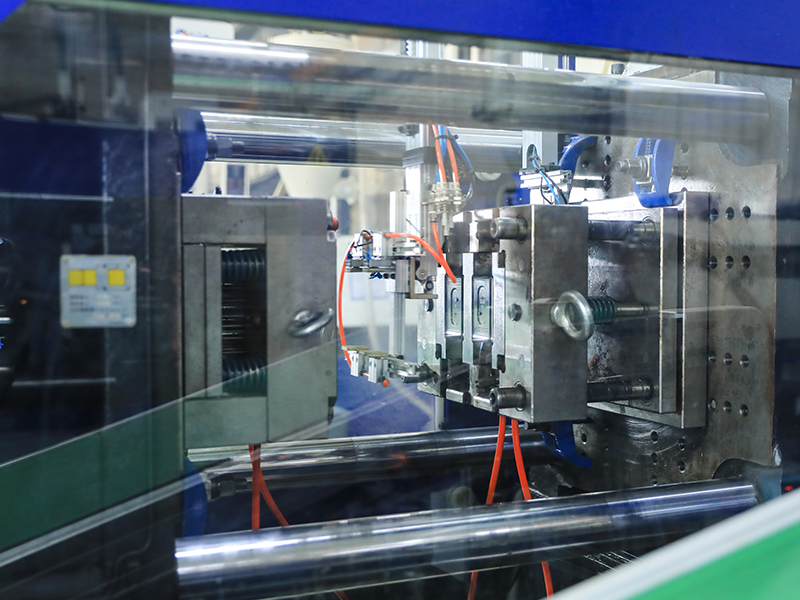
Holding time is the amount of time after injection that the pressure is maintained to allow the plastic melt to further fill the mold. This time also needs to be precisely controlled. Too long a holding time may result in over-compaction of the plastic, affecting the dimensional accuracy of the product, while too short a holding time may result in uneven shrinkage of the plastic, creating internal stress.
Control of holding time is critical to prevent product defects. It can help ensure that the shape and dimensions of the product are stable, while also reducing internal air bubbles and cracks.
Overall, injection and holding times are critical factors in the injection molding process. They need to be precisely adjusted to specific product requirements and production conditions. Only in this way can we produce products that meet functional requirements and have a good appearance.
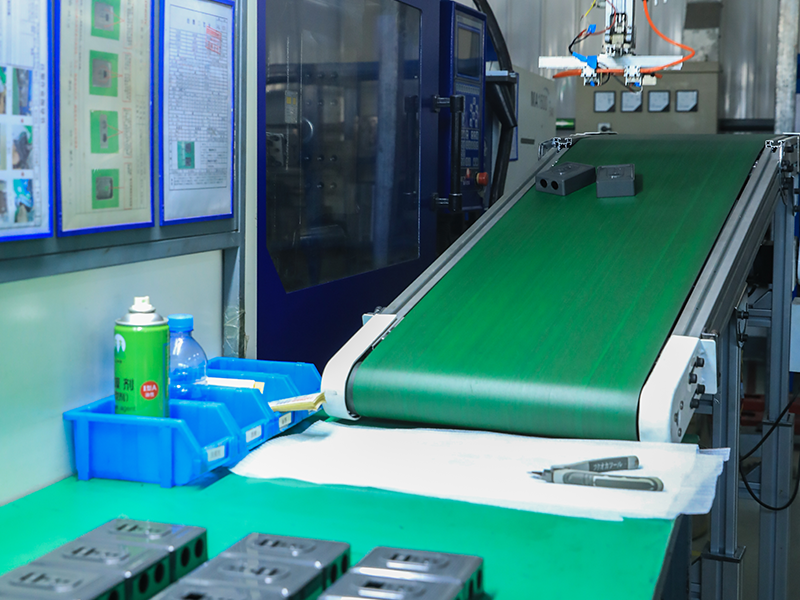
In this process, we need to constantly experiment and learn in order to find the optimal process parameters. This requires patience and care, as well as a deep understanding of injection molding processing. But when we succeed in finding that balance, we can create truly exceptional products.
The world of
injection molding processing is full of challenges, but also full of opportunities. If we are willing to invest the time and effort to understand and master it, we can succeed in this field.
Translated with DeepL.com (free version)