In
the modern medical field, the manufacturing of medical devices is a
precise and complex process, in which the shell injection molding
processing is a key step to ensure the safe, stable and efficient
operation of medical devices. In this process, the power source of the
push-out mechanism plays a crucial role. It is not only the embodiment
of physical force, but also the crystallization of technological
innovation and human wisdom.
Power source, as the name
suggests, is to promote the medical device shell injection molding
processing push the fundamental power of the operation of the mechanism.
This power source can be various, including hydraulic drive, motor
drive, pneumatic or mechanical drive. Each power source has its own
unique advantages and application scenarios, and together they form a
solid cornerstone of medical device manufacturing.
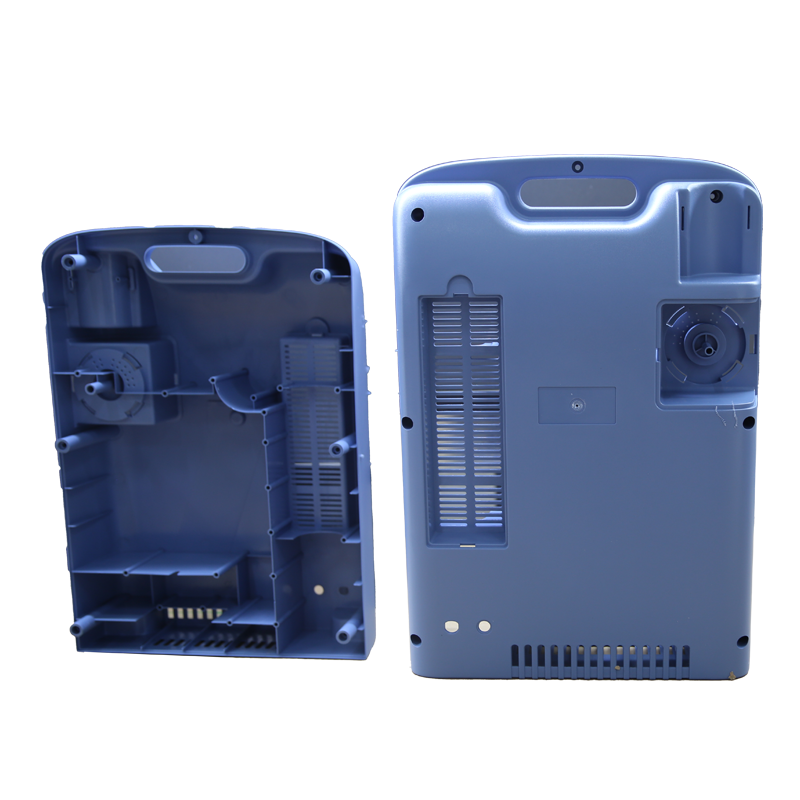
Hydraulic drive systems are known for their stability and powerful
thrust, providing continuous and uniform force during the injection
molding process to ensure the quality and precision of molded medical
device housings. This power source is particularly suitable for
applications where precision is critical, such as the manufacture of
pacemakers or neurostimulator housings.
Motor-driven systems
are favored for their high efficiency and energy-saving properties. With
fine electronic control, the motors can be precisely adjusted in terms
of push-out speed and force, adapting to complex and variable machining
requirements. This power source is suitable for high-volume production,
such as the manufacture of shells for disposable syringes or infusion
tubes.
Pneumatic drive systems are highly regarded for their
fast response and cleanliness. Pneumatic pressure is used as a power
transfer medium for fast motion execution and a contamination-free
operating environment. This power source is suitable for the production
of housings for medical devices that require high levels of hygiene,
such as surgical tools or labware.
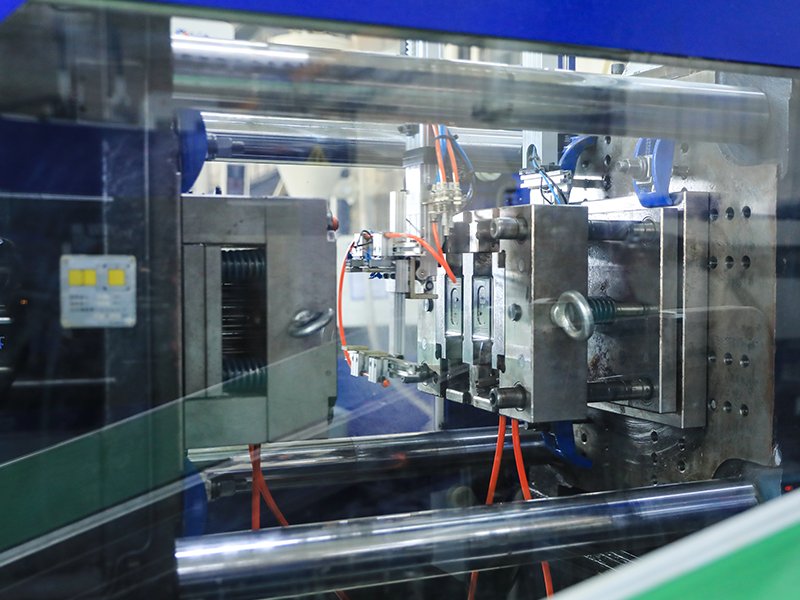
Mechanical drive systems, on the other hand, rely on precision gears
and transmissions for their reliability and durability. While mechanical
drives may not be as fast or flexible as other power sources, they
offer unrivaled stability and long-term performance guarantees in
heavy-duty and high-stress applications.
Regardless of the
power source, they are an integral part of the injection molding process
for medical device housings. They exist not only to enable physical
propulsion, but also to ensure the safety, reliability and efficiency of
medical devices. Behind every precision medical device, there is a
powerful power source silently supporting, they are the guardian of
medical innovation, is the guardian of human health.
Therefore,
when we talk about the power source of the medical device housing
injection molding processing launching mechanism, we are not only
discussing a technology or a device, we are also discussing an important
topic of life and health. Every advancement of these power sources is a
contribution to human well-being, and every innovation is a tribute to
the dignity of life.
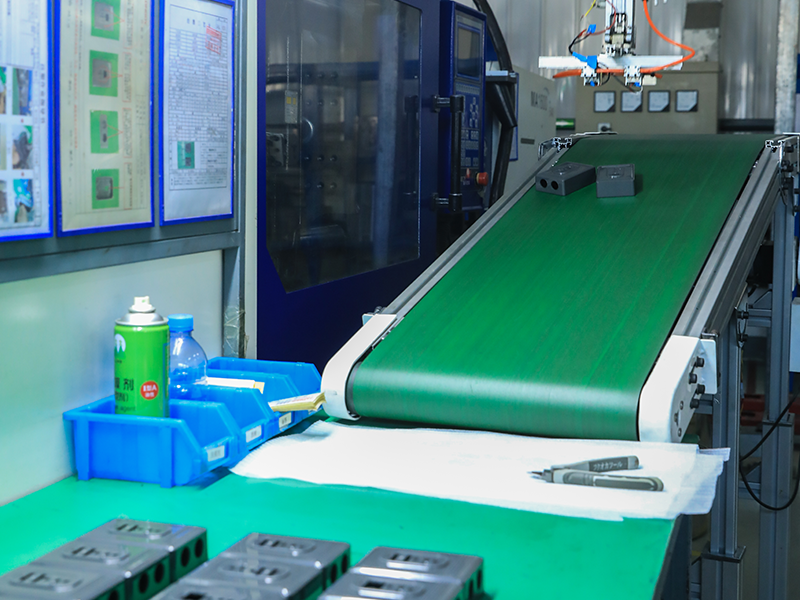
In the future, with the continuous progress of science and technology,
the power sources of medical device housing injection molding processing
will be more intelligent, precise and environmentally friendly. They
will continue to play an irreplaceable role in the medical field,
contributing to human health and bringing hope and light to the world.