In the world of plastic products, transparency is a symbol of quality, which represents pure and flawless, crystal clear. However, even the most sophisticated injection molding process will inevitably encounter those headaches of transparent defects. These defects, like stains on a work of art, are impossible to ignore. Today, let us go deep into this quest for perfection, to unveil the secrets behind the transparent defects of injection molded products.
First of all, we need to understand is that the transparency of the level is not accidental, it is the material, process and the environment of the results of the joint role. When an injection molded product transparent defects, it is like a mirror reflecting some of the flaws in the production process. These defects may originate from a number of aspects, and our analysis will start from the following key points.
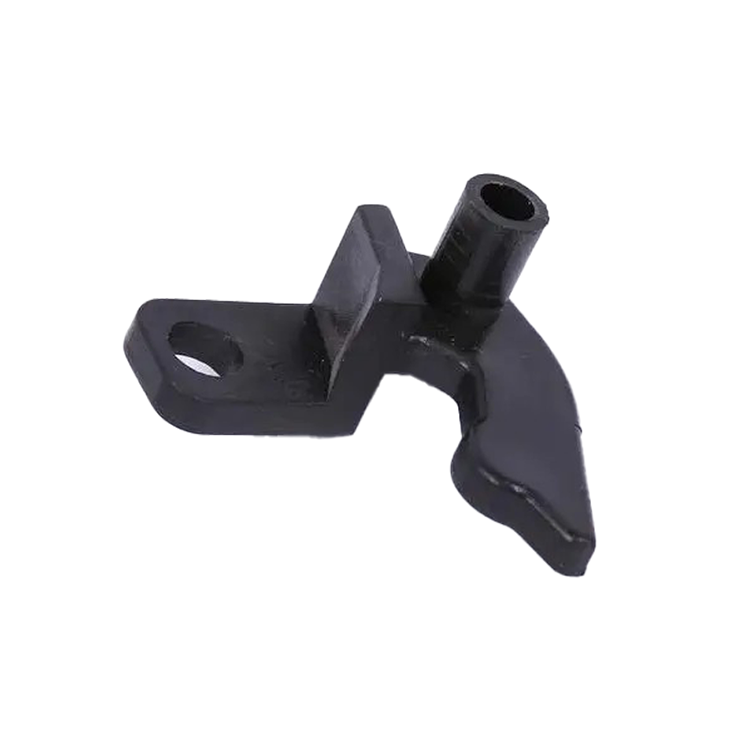
The first is material selection and handling. The base material for injection molded products is usually plastic pellets, and the quality of these pellets directly affects the transparency of the final product. If the raw material contains impurities or is insufficiently dried, then bubbles or cloudy opaque areas will be created during the high temperature and high pressure injection molding process. Therefore, selecting high-quality raw materials and ensuring that they are adequately dried is the first step in ensuring transparency.
The next step is the tuning of the injection molding machine. Precise control of parameters such as temperature, pressure and injection speed of the injection molding machine is critical to the transparency of the product. Too high a temperature may cause the material to decompose, while too low a temperature may cause the material to plasticize insufficiently, affecting transparency. Similarly, improper injection speeds may lead to the creation of internal stresses, resulting in visible defects.
Environmental factors should not be ignored either. Dust, humidity and temperature fluctuations in the production environment can all have an impact on the injection molding process. Dust can become the core of impurities, high humidity can lead to moisture absorption in the material, and temperature fluctuations can affect the stability of the material. Therefore, a clean, constant temperature and humidity production environment is key to ensuring transparency.
Finally, mold design and maintenance are also important factors in determining transparency. The precision of the mold is directly related to the surface quality of the product. Any tiny scratches or abrasions may leave traces on the transparent products. Therefore, regular maintenance and polishing of the mold is an important measure to maintain transparency.
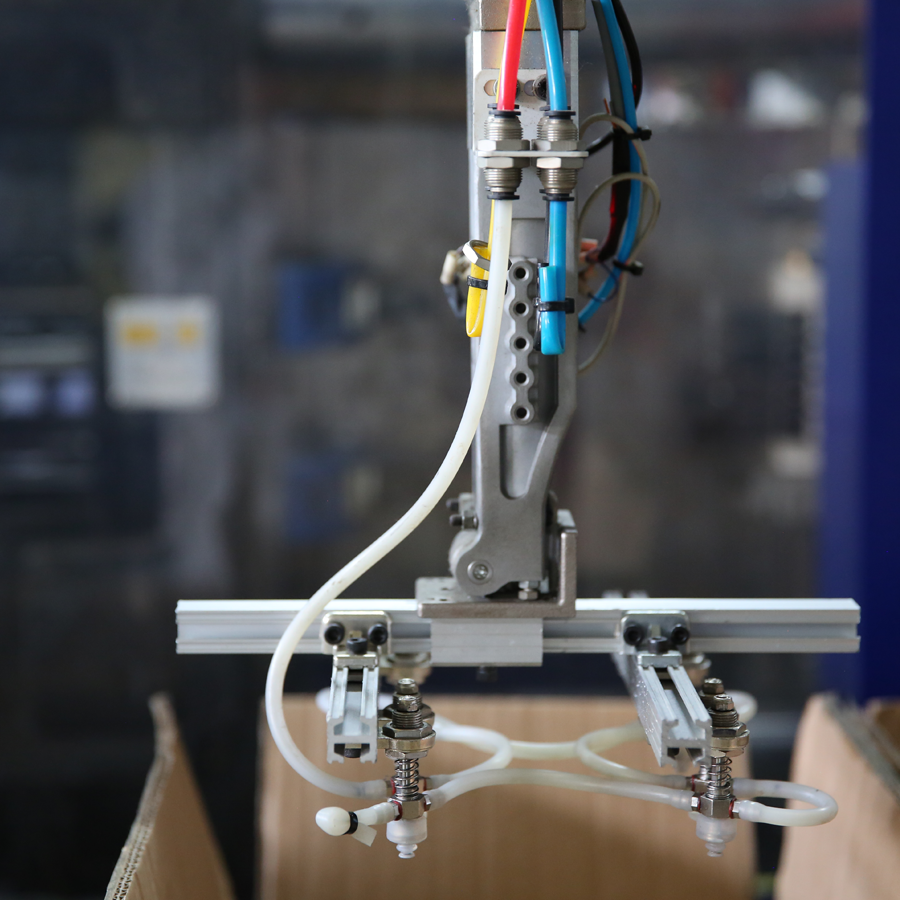
Through the above analysis, we can see that the transparent defects of injection molded products are not untraceable. Every detail may become the key to influence the transparency. From the selection of raw materials to the tuning of the injection molding machine, from the optimization of the production environment to the fine polishing of the mold, every step requires us to strive for excellence and the pursuit of perfection.
In this quest for perfection, we are not only solving the problem of transparency defects, but also improving our understanding of the process and the pursuit of quality. Every success is a challenge to technology and a respect for details. Let's continue our exploration in this transparent world and go beyond until we reach perfection.