In this era where precision and efficiency are king,
injection molding is not only a means of production, but also a process art in pursuit of perfection. Each injection molded product is the crystallization of the designer's wisdom, the embodiment of the engineer's technology, and the testimony of the operator's craftsmanship.
First of all, the choice of material is the soul of injection molding. High-quality plastic granules, like the artist's pigments, determine the texture and performance of the product. Different types of resins, such as ABS, PP, PE, etc., give the product different characteristics, from tough and durable to soft and flexible, each material has its own unique use and expressive power.
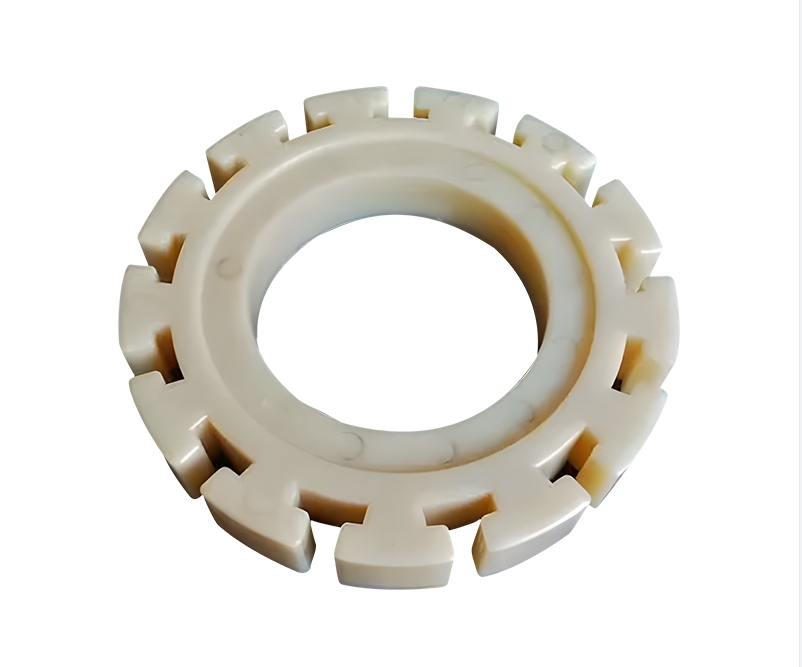
The design stage, on the other hand, is the arena of conceptualization and innovation. Mold designers must have an in-depth understanding of the product's usage environment and functional requirements, and transform complex geometric shapes into blueprints of molds that can be actually produced. This requires a deep understanding and application of specialized knowledge of rheology, cooling systems, gate locations, and so on.
And with the roar of the
injection molding machine, temperature control becomes the guardian of accuracy. The melting and flow of plastic is a sensitive process, and small fluctuations in temperature can lead to product defects. Therefore, a precise temperature control system is the key to ensuring product quality.
The regulation of injection pressure and speed are like a baton waved by a conductor, they determine the speed and strength of the plastic filled mold. Too fast or too slow speed, too much or too little pressure will affect the internal structure and appearance of the product quality.
Cooling and demolding is the final stage of injection molded parts processing, but also the test results of the moment. The length of cooling time directly affects the dimensional stability and stress state of the product. The smoothness of demolding tests the precision of mold design and manufacturing.
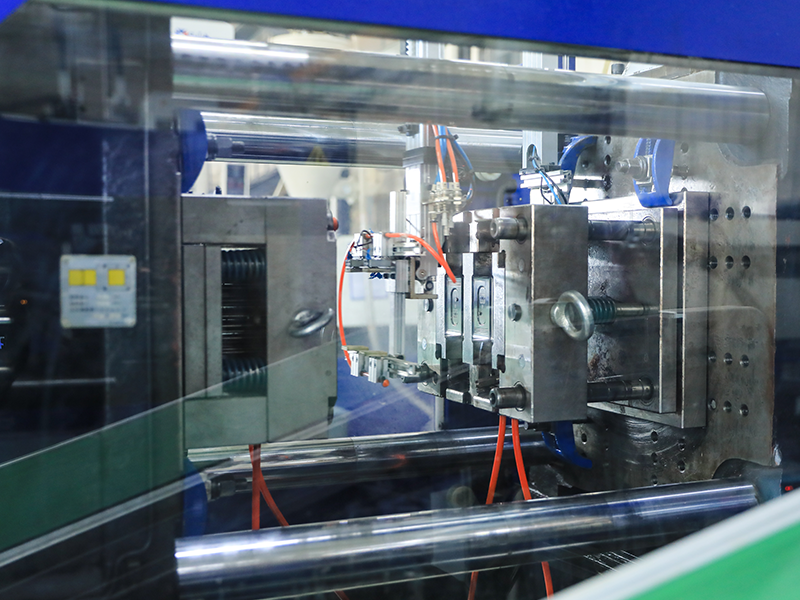
In the whole injection molded parts processing process, each link can not be ignored, each step requires careful planning and implementation. This is not only scientific rigor, but also the pursuit of perfection. Each finished injection molded part is a respect for details, a love of craftsmanship and a commitment to quality.
In this fast-changing world, the essentials of
injection molded part processing remind us that no matter how much technology advances, respect for the underlying craftsmanship and a commitment to excellence are always the unchanging rules of manufacturing success. By practicing these essentials, we are not only able to shape products in physical form, but also convey the contemporary value of craftsmanship.