Electrical stamping parts processing: details determine the king of quality
The processing of electrical stamping parts is a key process, which directly affects the quality and performance of electrical parts. In the electrical appliance manufacturing industry, stamping parts, as important structures and connectors, play a vital role. However, due to the high complexity and strict requirements of processing electrical stamping parts, there are many details that need to be paid attention to. This article will give you a detailed introduction to the precautions for processing electrical stamping parts to help you ensure the production of high-quality electrical parts.
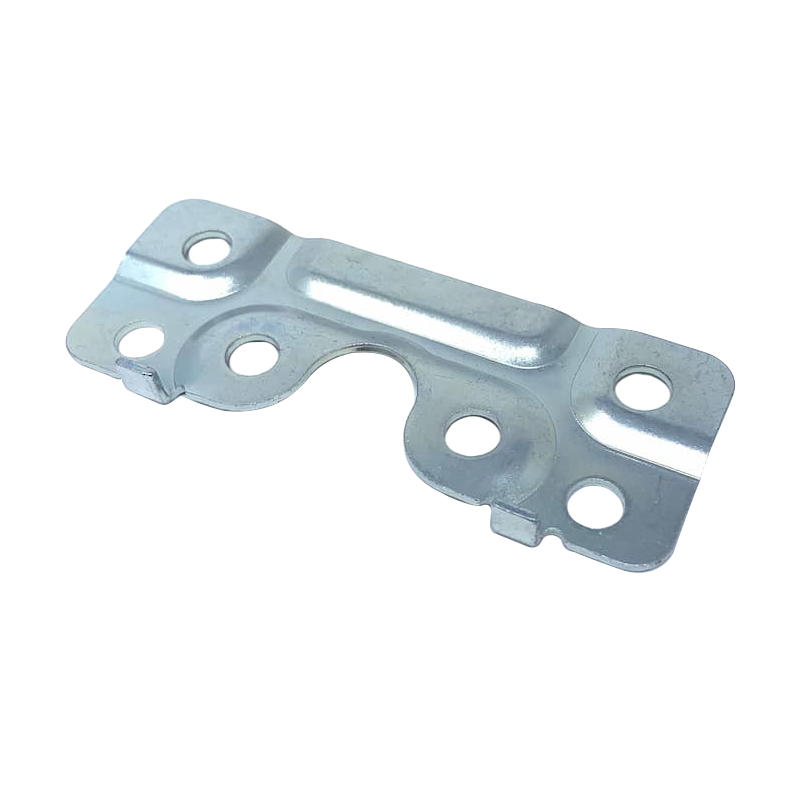
1. Selection of materials
Material selection for electrical stamping parts is crucial. Common materials include stainless steel, aluminum alloy, etc. Different materials have different characteristics and performance, and appropriate choices need to be made based on the usage environment and requirements of the appliance. At the same time, the quality and supply channels of materials are also one of the key factors that determine the quality of stamping parts processing. High-quality materials should be selected and partnerships should be established with reliable suppliers to ensure the stability and reliability of the materials.
2. Mold design and manufacturing
Molds are required when processing stamping parts. The design and manufacturing of the mold directly affect the quality and cost of the product. When designing the mold, it is necessary to consider the shape, size, holes and other details of the electrical stamping parts, and reasonably set the structure and process parameters of the mold. During the mold manufacturing process, every link should be strictly controlled to ensure the accuracy and stability of the mold. Only through excellent mold design and manufacturing can stamping parts with high precision and consistency be produced.
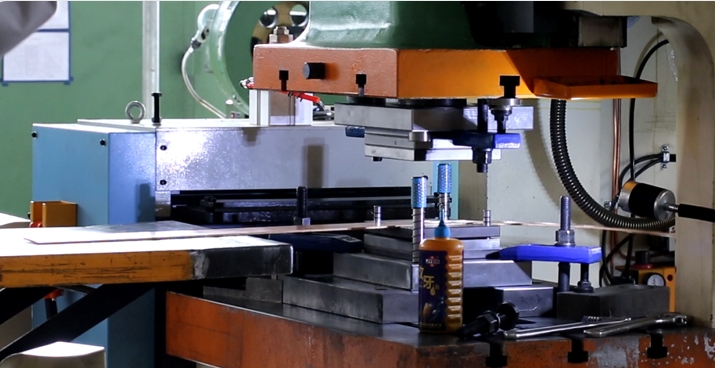
3. Optimization of processing technology
The processing of electrical stamping parts requires consideration of many factors, such as the selection of punch machines, installation of molds, punching sequence, etc. Reasonable selection of punch type and punch parameters, appropriate process flow arrangement and strict process operations can effectively improve the quality and processing efficiency of stamping parts. In addition, quality control points during processing need to be clarified and strict quality inspections implemented to ensure that products meet design requirements.
4. Surface treatment of stamping parts
Surface treatment of electrical stamping parts is an important part of ensuring product appearance and corrosion resistance. Common surface treatment methods include electroplating, spraying, etc. According to the usage environment and requirements of electrical appliances, select the appropriate surface treatment method and strictly control the surface treatment process parameters to avoid problems such as delamination and oxidation, and ensure that stamping parts have good surface quality and corrosion resistance.
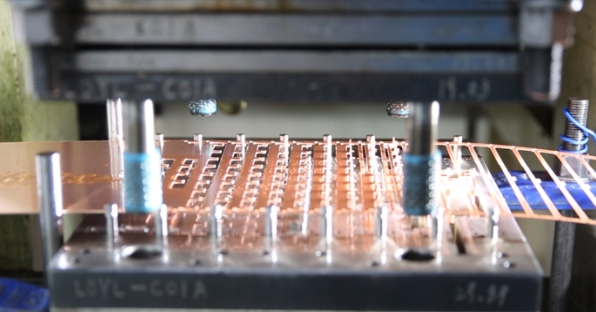
5. Strict quality control
In order to ensure the quality of electrical stamping parts processing, strict quality control measures need to be implemented. From the inspection of raw materials to the monitoring of each processing link to the inspection of final products, quality control requirements need to be strictly implemented. In addition, it is necessary to establish a complete quality tracking system to detect and deal with problems in a timely manner to continuously improve product quality and stability.
To sum up, the processing of electrical stamping parts is very detail-oriented. Only by paying attention to every aspect can we produce high-quality electrical parts. From material selection, mold design and manufacturing, processing technology optimization, to stamping parts surface treatment and strict quality control, every detail requires sufficient attention. Only by continuously improving and improving process levels can we meet the market's demand for product quality.